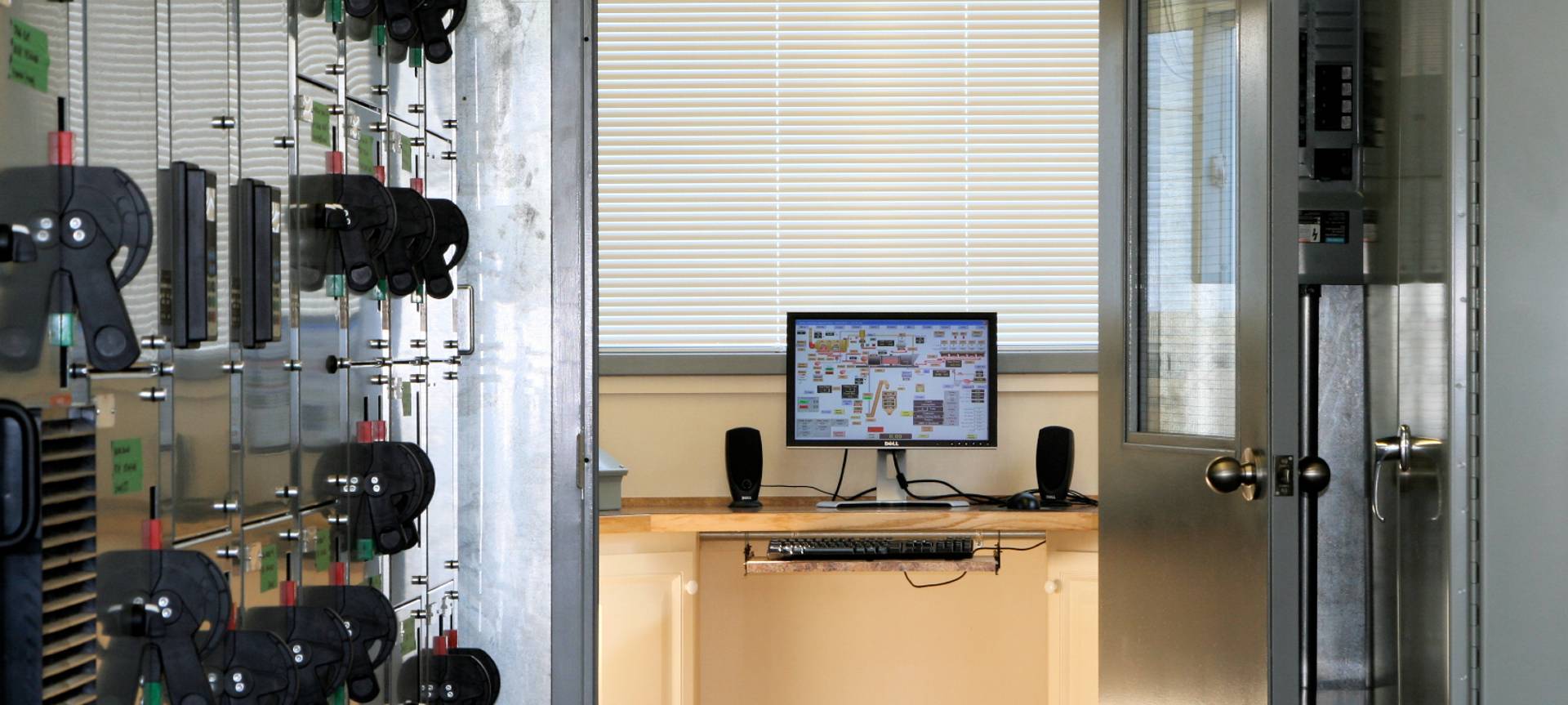
Control Panels
Aggregate process
An aggregate process’s effectiveness and efficiency can be enhanced by installing bespoke controls. They allow for a higher degree of automation and control over the manufacturing process, which boosts output while maintaining or even improving quality.
Sand classifier process
Personalized Regulations, Summarized Separating and classifying aggregate particles of different sizes is the goal of the sand classifier process. Sand that is too large or too small for construction can be separated using this method. Utilizing screens and physical processes like tumbling and vibrating, particles are separated and sorted. The method is designed to remove any particles that are too large or too small to be used in construction projects, ensuring that only the best material is used. To remove contaminants like dirt and dust, this technique is also employed. High-quality aggregate materials for building projects rely substantially on this technique’s production.
Automatic stacking
To speed up the process of piling on components, engineers developed a set of tools known as aggregate custom controls. They allow one to regulate the size, form, and placement of stacked items. As an added bonus, they can be utilized to guarantee a neat and orderly stack every time. Costs of time and effort for manual stacking can be reduced with the help of aggregate custom controls. They can also be used to make sure everything is lined up and in the right place. Structures that are both sophisticated and necessary in the building and engineering industries can be designed using aggregate custom controls. They can be utilized in the manufacturing sector to aid in the creation of large scale components.
Crusher diagnostics
Aggregate custom controls crusher diagnostics are designed to provide feedback on the overall performance of the aggregate crusher equipment. The system can detect potential problems with the equipment and provide a detailed analysis of the current condition of the machine, including identifying and diagnosing faults, monitoring wear and tear, estimating remaining useful life, and providing maintenance advice. The diagnostics system can be used to prevent unexpected downtime, reduce maintenance costs, and increase the productivity of the aggregate crusher.
Weight and loadout
Aggregate custom controls weigh and loadout are used to accurately measure and monitor the weight of the aggregate materials while they are being loaded onto a truck or other transport vehicle. This type of system is especially useful for large production facilities where materials must be weighed and loaded quickly and efficiently. The aggregate custom controls weigh and loadout system offers precise and accurate readings so that materials can be loaded and transported without any delays or issues. This system also helps to minimize overloading and minimize the risk of product damage due to incorrect loading. The system also helps to reduce personnel costs and improve productivity.
Inventory Control
Aggregate inventory control refers to the process of overseeing stock levels at every location. It’s a method for making sure companies never have too little stock or too much, based on client demand. As part of this process, you need to keep tabs on stock levels in various storage facilities, examine data for patterns, and make strategic choices. Companies can save money and time with the help of aggregate inventory control because it cuts down on wasted goods and storage space. It helps firms anticipate your needs and prepare for future purchases.
Maintenance Logging
Aggregate maintenance logging is the process of recording and keeping track of the maintenance and repair of an aggregate, such as a construction site or a road network. This helps ensure that all maintenance and repair activities are properly documented and can be accessed by those responsible for managing the aggregate. The log can include information such as the date, location and type of maintenance, who carried out the work, and the cost associated with the repair. It can also include any other relevant details such as the materials used, the duration of the repair, and any other observations. By keeping an accurate and up–to–date log, organizations can identify potential problems and take corrective action in a timely manner.
Production reporting
Collecting, evaluating, and reporting information on aggregate production. This information is compiled from a variety of sources and may include production prices, quality control procedures, safety procedures, and environmental requirements. Reporting on production as a whole entails keeping tabs on production trends and using data analysis to spot problem spots. Businesses utilize production summaries to monitor resource utilization, spot inefficiencies, and locate cost-cutting opportunities. It’s a must-have for companies who want to keep their operations effective and trouble-free.
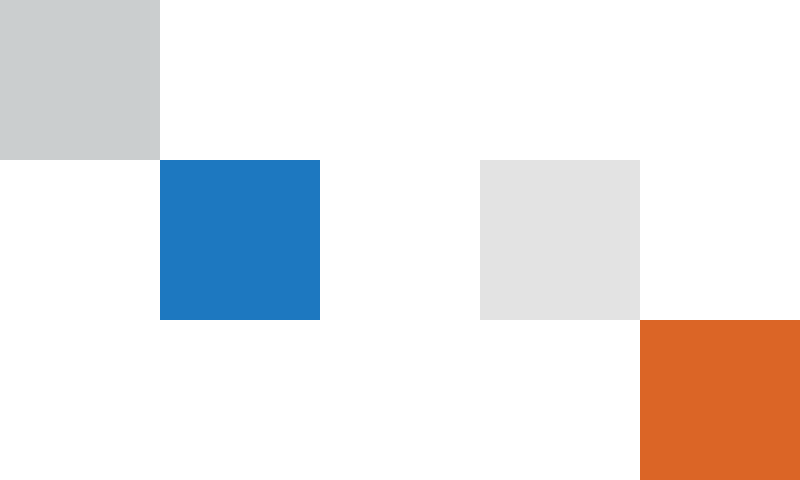
Our services form a complete electrical/automation package of design, installation, maintenance and service.
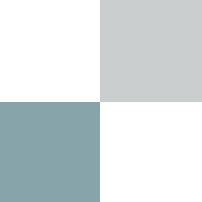
At Harley’s Electrical, we strive to provide our customers with an affordable solution without compromising on quality.
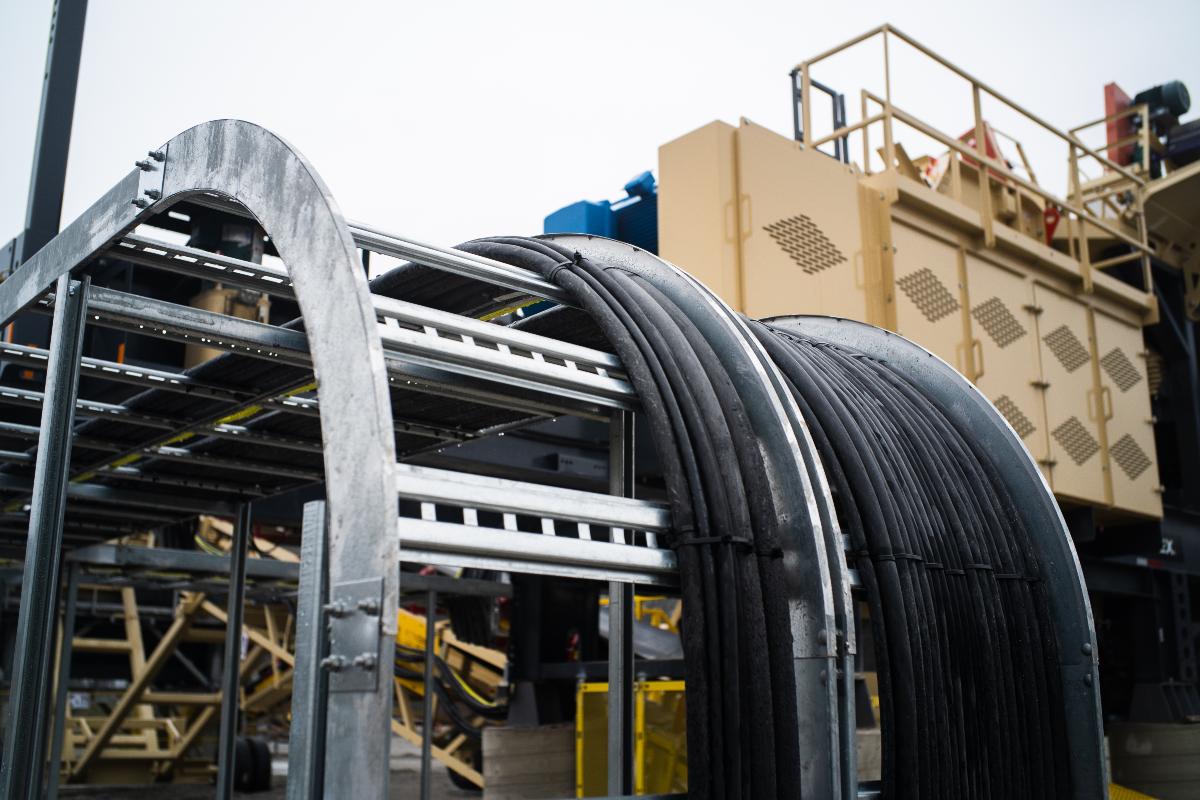
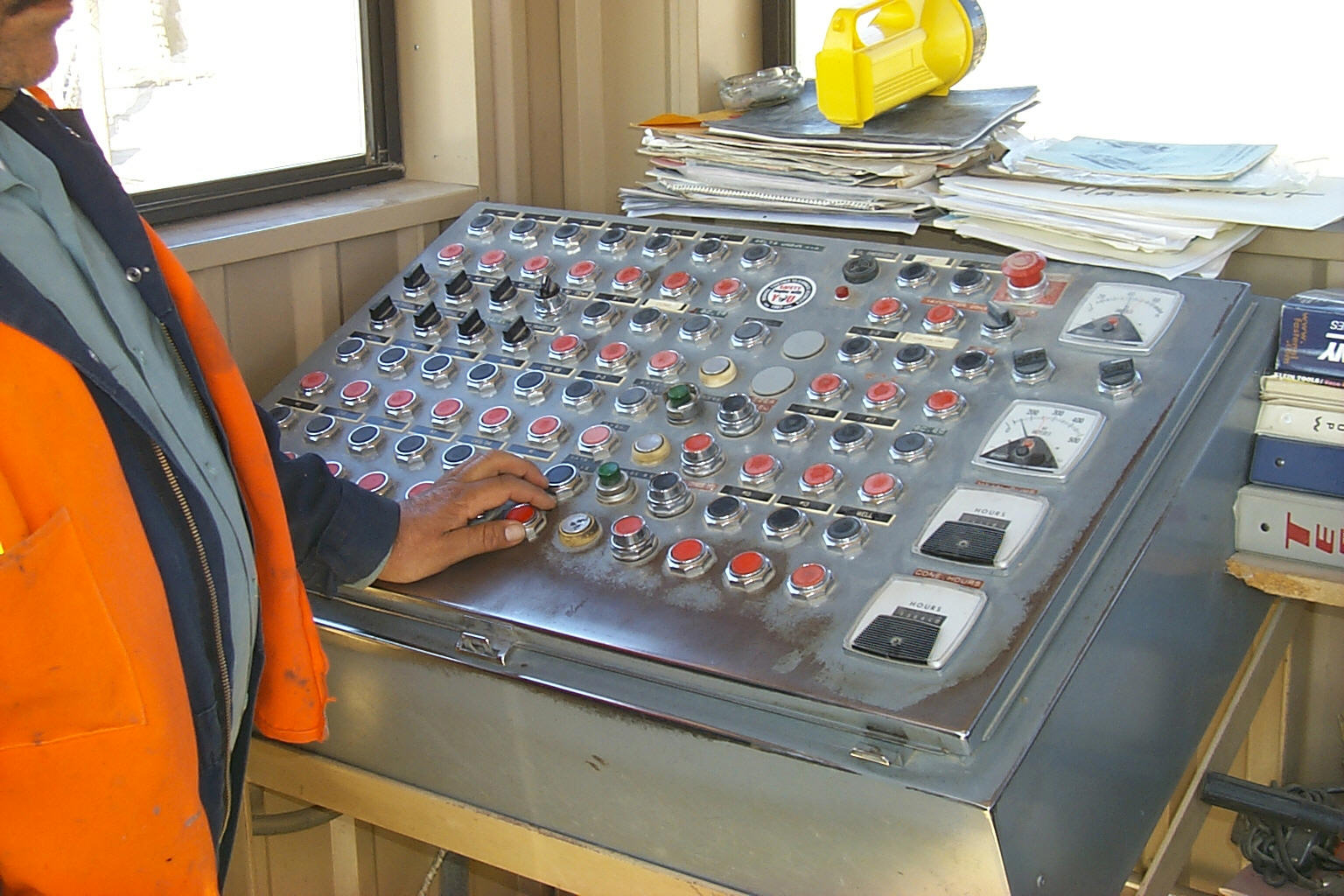
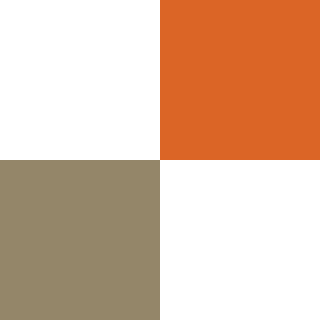